River 150 | 10-15 Metric Ton Amphibious Excavator For sale
This 10-15 ton amphibious excavator is engineered for optimal performance in wet and muddy conditions, offering exceptional stability and efficiency. Its superior buoyancy and traction ensure reliable operation in challenging environments.
Features of 10-15 ton amphibious excavator
- Adaptability: Designed for 12-15 ton excavation.
- Extendable Undercarriage: Adjustable width from 2.8 meters to 4.4 meters, allowing flexibility in various work environments.
- Versatility: Suitable for both narrow and wide working conditions.
- Cost Efficiency: Reduces construction costs by accommodating diverse operational needs with a single machine.
- Transport Convenience: Easier transportation on width-limited roads.
- Reduced Assembly Work: Eliminates the need for frequent disassembly and reassembly of the machine.
Descriptions of 10-15 Ton Amphbious Excavator
10-15 ton amphibious excavator is equipped with pontoons or specially designed tracks that allow it to operate on water and soft, marshy terrain, in addition to standard land surfaces. The 10-15 ton classification refers to its operational weight, making it suitable for medium to heavy-duty tasks such as dredging, land reclamation, and construction in wetlands. Its design ensures stability and mobility in challenging conditions, offering a balance between power and maneuverability.
The RS150-A pontoons are designed specifically for 12-15 ton excavators, offering a versatile undercarriage that extends from 2.8 to 4.4 meters in width. This innovative design enhances the excavator’s ability to operate efficiently in both narrow and wide environments, reducing construction costs and simplifying transportation on width-restricted roads. Additionally, it minimizes the need for disassembly and reassembly, making it a convenient choice for dynamic work sites.
Specifications of 10-15 Ton Amphibious Excavator
River150 | Parameter | Unit |
a) Overall machine length | 10040 | mm |
b) Overall machine width without side pontoons | 3810 | mm |
c) Overall machine height(to boom) | 3710 | mm |
d) Turntable width | 2490 | mm |
e) Single pontoon length | 6880 | mm |
g) Track shoe width | 1020 | mm |
m) Single pontoon height | 1590 | mm |
f) Pontoon overall width | 3810 | mm |
i) Track gauge | 2560 | mm |
h) Distance between sprocket and idler | 6110 | mm |
j) Counterweight ground clearance | 1740 | mm |
k) Min ground clearance | 1060 | mm |
l) Max turning radius of the tail | 2824 | mm |
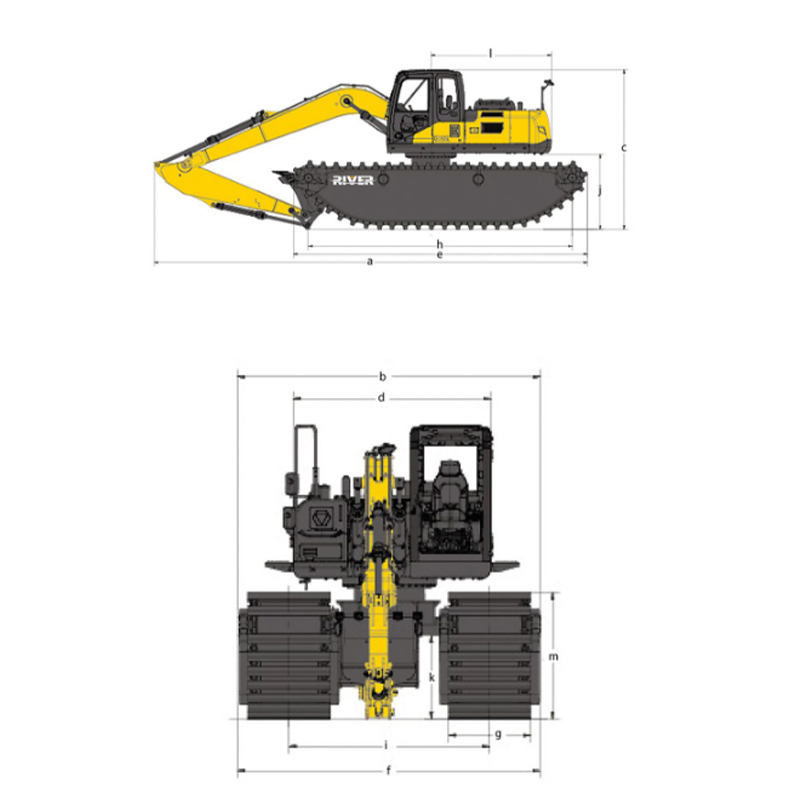
River150 | Parameter | Unit |
L1) Max digging radius | 9840 | mm |
L2) Max digging height | 10990 | mm |
L3) Max digging depth | 5890 | mm |
L4) Max unloading height | 8525 | mm |
L7) Min turning radius | 2970 | mm |
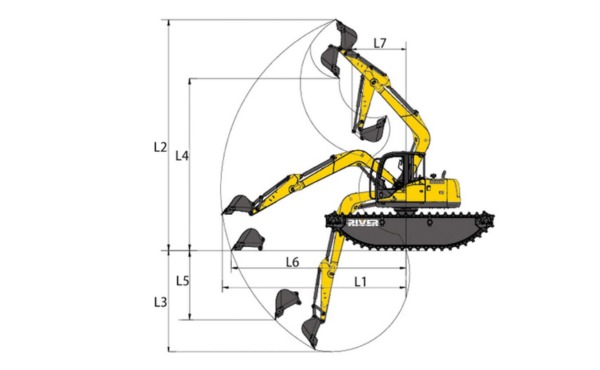
River150 | Parameter | Unit |
Pontoon Model | RV150-3 | / |
Operating weight | 21500 | Kg |
Boom and stick length | 8621 | mm |
Bucket capacity | 0.6 | m³ |
Engine model | CumminsQSF3.8 | / |
Rated power/speed | 86/2200 | Kw/rpm |
Max torque/speed | 470/1300 | Nm/rpm |
Displacement | 3.8 | L |
Motor model | TM22 | Mottrol(Doosan) |
Output torque | 2616 | N.m(kgf.m) |
Continuous pressure | 350 | MPa(kgf/cm2) |
Driving speed | 2.9 | km/h |
Swing speed | 11 | r/min |
Gradeability | 《30° | ° |
Ground specific pressure | 22.8 | kPa |
Bucket digging force | 77 | kN |
Stick digging force | 48.8 | kN |
Fuel tank volume | 760 | L |
Hydraulic oil tank volume | 105 | L |
Engine oil capacity | 11 | L |
- The above specification is based on XE160SL excavator model with 9m long reach front, actual working range may vary from different excavator models.
Why Choose RIVER’s 10-15 Ton Amphibious Excavator?
Our Lightweight Design was developed by our construction team’s over 15 years of experience in water projects, which means the pontoon buoyancy is less than the total machine weight (the upper structure and undercarriage of the excavator). By doing so, the amphibious excavator can work in shallow water and gain better flexibility under 1.8 meters (depending on the model).
- The excavator can land and manoeuvre stably in shallow water. All digging operations in different directions are as safe as land crawlers working on the ground without risk of rolling over;
- With a Lightweight Designed pontoon, customers enjoy a more compact appearance, easier marsh travel, and more flexible operation while saving on investment costs.
- A systematic series of side pontoons and spuds provided for pairing with different undercarriage models would allow the amphibious excavator to fully float in deeper water ranging from 1.6 meters to a maximum of 5 meters, which enables swamp buggy working in diversified work scenarios.
∗ Specialized Track Shoes Material
As the most essential wear part, the track shoe cleats we produce are of China WISCO’s super high strength welding structure steel HG785D whose yield strength is 685MPa and tensile strength is 785MPa. Its impact energy under -20℃ is above 47J, and it enjoys good weldability and formability. The same material is selected for reinforcing the conjunction part of the pontoon’s side plate and top plate which is one of the key parts deciding the framework’s firmness. We choose stronger material than any other competitors around the world to effectively avoid the pontoon structure from deformation, and wins exceedingly high comments from customers about our track shoe cleats’ wearability and durability.
∗ Track Chain Roller
We choose 40Cr steel (DIN 41Cr4) for our track chain rollers which are one of the important wear parts during excavator’s daily operation. All rollers must go through heat treatment including quenching and tempering to enhance the hardness to HRC50-56.
∗ Wear Pad for Resistance
We choose special wear-resistant material NM400 for the wear pad to ensure it would not be easily worn out by the track chains. High-class material selection of the wear pad will extend the pontoon’s lifetime by 1-2 years on average.
∗ Screws Adopted for Amphibious Excavator
All screws equipped on our swamp buggy are treated with Dacromet process, and must go through salt spray test which lasts for 1000 hours. This highly improves the anti-corrosion ability of the screws, and thus allows the excavator to work longer in more severe working environment. The maintenance and replacement cycle of spare parts are thus extended.
∗ Hydraulic Oil Pipes & Fittings
Both the hydraulic oil pipes and fittings are of imported famous brands with good durability. And the external surface of all oil pipes are wrapped with a protective PVC layer to enhance its anti-corrosion and wear-resistant ability. All oil pipes are arranged in good oder with tidy layout.
∗ Guide&Drive Wheel Heat Treatment
The front idler and the drive sprocket both go through special heat treatment to ensure reliable hardness and strength.
∗ Steel Plate Shearing & Bending
All the plate bending is done by China’s top brand NC press brake machine which ensures high accuracy and unified bending curves. While thick steel plates are cut by plasma cutting machine, thin plate cutting is done by laser cutting machine, both quick and accurate with the cutting edge in good order without any iron scurf.
∗ Robot Welding of Pontoon Undercarriage
All the buckets and part of our pontoon undercarriage are automatically welded by the robot arm, especially spot welding areas. This not only ensures high welding accuracy, but also helps improve the entire productivity as well as reduce resource consumption and possible environment pollution.
∗ H-frame Machining
We customize every H-frame in accordance to the slewing bearing dimensions of different excavator brands and models. Each H frame is machined as a whole by a gantry type machining center and the circle of bolting holes are milled by the hole milling machine. This secures accurate matching for complete assembly and also enhances the overall parts consistency of the amphibious excavator, which will provide better operation feedback for the operators.
∗ Compartment Gastight Test
After welding, all the three vacuum chambers of the pontoon must receive gastight testing where 4 standard atmospheric pressure will be charged and held for 15 minutes. Only ensured no leakage by the test as well as proved qualified by other examinations will our amphibious excavators be allowed to leave the factory.
∗ Amphibious Pontoon Painting
A fully automatic shot-blasting and painting line which cost USD12.5 million is running for our pontoon’s surface treatment from rust removing, shot-blasting, polishing, puttying, priming to top finishing, and the coating surface is even and smooth. The paint we use is specialized type for marine ship coating which is hard, wearable with good gloss and not easy to peel off. Each pontoon must go through shot blasting till Sa2.5 grade with surface roughness within 30-70um before getting coated. The thickness of coating layer on the pontoon undercarriage must achieve 160~200um and each pontoon must have 2 layers of primer and two layers of top coats.
∗ Professional Swamp Buggy Assembly/Disassembly Workshop
We have a professional and skilled crawler excavator workforce team for disassembling the chassis and assemblying our pontoon undercarriage with the upper body. With their strict technical standards for motor positioning, hydraulic oil pipeline installation, and bolt/screw tightening, etc, our amphibious excavators’ installation precision is highly assured. Every set of RIVER’s excavator will also have a travel test and conventional commissioning before delivered to our customer.
Applications of 10-15 Ton Amphibious Excavator
The 15-ton amphibious excavator is a robust machine designed for medium-sized excavation tasks. With its moderate digging power, it excels in both land and water environments. Ideal for environmental management, such as wetland restoration, flood control, and smaller-scale dredging projects, this excavator is well-suited for construction projects involving soft ground or shallow water.
Enhanced Mobility and Maneuverability
One of the standout features of the 15-ton amphibious excavator is its maneuverability in tight spaces and smaller water bodies. Its compact size provides excellent access to confined areas and allows for intricate work in sensitive environments.
Cost-Effective and Economical
The 15-ton amphibious excavator offers a lower initial cost, making it a cost-effective choice for smaller-scale projects. It provides an economical solution where high capacity is not the primary requirement.
Ease of Maintenance and Transport
Maintenance for the 15-ton amphibious excavator is generally easier and less expensive due to its smaller size. Additionally, it is often more straightforward to transport and set up on-site, reducing logistical challenges.
Ready to Enhance Your Project with a 15-Ton Amphibious Excavator?
Are you working on a project that involves wetlands, soft terrain, or shallow water? The 15-ton amphibious excavator is your perfect solution. With its unmatched mobility, cost-effectiveness, and ease of maintenance, it’s designed to tackle medium-sized projects efficiently. Contact us today to learn more about how our 15-ton amphibious excavators can elevate your project. Our experts are ready to assist you with the best solutions tailored to your needs.