AMPHIBIOUS UNDERCARRIAGE
Amphibious Excavator Undercarriage & Its Attachments
Amphibious undercarriage (pontoon undercarriage) redefines versatility in amphibious equipment, enhancing stability and maneuverability for amphibious excavators and marsh buggy units. It experiences unparalleled performance in wetland terrains. RIVER’s amphibious excavators can adapt to various brands and models of upper excavators, ranging from 5 tons to 40 tons. Our amphibious undercarriage excavator and its attachments are designed to elevate your excavation projects with advanced technology and robust performance.
What is an Undercarriage for Amphibious Excavator?
An amphibious undercarriage is a specialized undercarriage system designed to enable excavators and other heavy machinery to operate efficiently in both water and on land. This system is particularly beneficial for work in challenging terrains such as swamps, marshes, wetlands, and shallow water bodies.
Amphibious Undercarriage Attachments
Additional side pontoons of an amphibious excavator, also known as additional pontoons or floating pontoons, are crucial attachments that enhance the stability and buoyancy of the amphibious excavator when operating in water. These pontoons are elongated, floatation devices mounted on the sides of the amphibious excavator’s undercarriage, extending its capability to tackle deeper and more turbulent aquatic environments.
Hydraulic positioning piles are a type of deep foundation system, utilizing hydraulic mechanisms to install piles deep into the earth to support structures by transferring their load to layers of soil or rock that have sufficient bearing capacity. They are crucial in construction and civil engineering projects, offering a robust solution for establishing foundational support where shallow foundations are not feasible due to poor soil conditions or when the structure is subject to heavy loads.
Key Features of Amphibious Undercarriage
Specially designed pontoons provide stability and flotation on water surfaces.
Robust materials resist wear and corrosion for longevity in harsh environments.
Allows seamless transition between land and aquatic settings, improving access to difficult terrains.
Wide track shoes minimize ground pressure, protecting sensitive ecosystems during operations.
HG785D High-Grade Steel ensures exceptional strength-to-weight ratio for structural integrity and durability.
Epoxy zinc-rich paint enhances strength and lifespan, resisting corrosion and abrasion in extreme conditions.
Benifits of Using Amphibious Excavator Undercarriage
- Versatility in Terrain: The amphibious undercarriage allows excavators to transition seamlessly between land and water. This versatility is crucial for projects involving dredging, waterway maintenance, and construction in swampy areas.
- Improved Stability: The buoyant pontoons and extended tracks provide increased stability on soft and unstable ground, reducing the risk of the machine tipping over or getting stuck.
- Increased Accessibility: Excavators equipped with amphibious undercarriages can access and work in areas that are otherwise inaccessible to standard machines, such as marshes, lakes, and coastal regions.
- Enhanced Safety: By maintaining stability and preventing the excavator from sinking or tipping, the amphibious undercarriage enhances operator safety, especially in hazardous working environments.
- Efficiency and Productivity: The ability to work in both water and on land without the need for multiple machines or frequent repositioning boosts overall efficiency and productivity on the job site.
- Environmental Impact: Amphibious undercarriages can minimize environmental disruption by reducing the need for extensive land-based support and infrastructure in sensitive ecosystems like wetlands.
Optional Amphibious Undercarriage – Customized Configurations From China Supplier
Advantages of Amphibious Excavator Fabricated by RIVER :
PONTOON UNDERCARRIAGE MATERIAL
Specialized Track Shoes Material
As the most imperative wear part, the track shoe cleats we produce are of China WISCO’s super high strength welding structure steel HG785D whose yield and tensile strengths are 685MPa and 785MPa respectively. Its impact energy under -20℃ is above 47J, and it enjoys good weldability and formability. The same material is selected for reinforcing the conjunction part of the pontoon’s side plate and top plate which is one of the key parts deciding the framework’s firmness. We choose stronger material than any other competitors around the world to effectively avoid the pontoon structure from deformation and win exceedingly high comments from customers about our track shoe cleats’ wearability and durability.
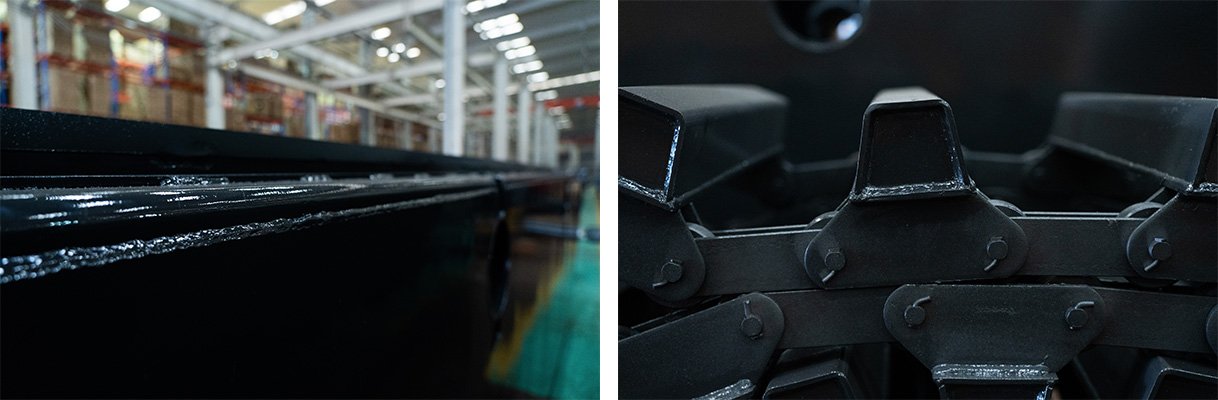
Track Chain Roller
We choose 40Cr steel (DIN 41Cr4) for our track chain rollers which are one of the most critical wear parts during the excavator’s daily operation. All rollers must be put through heat treatment including quenching and tempering to enhance the hardness to HRC50-56.
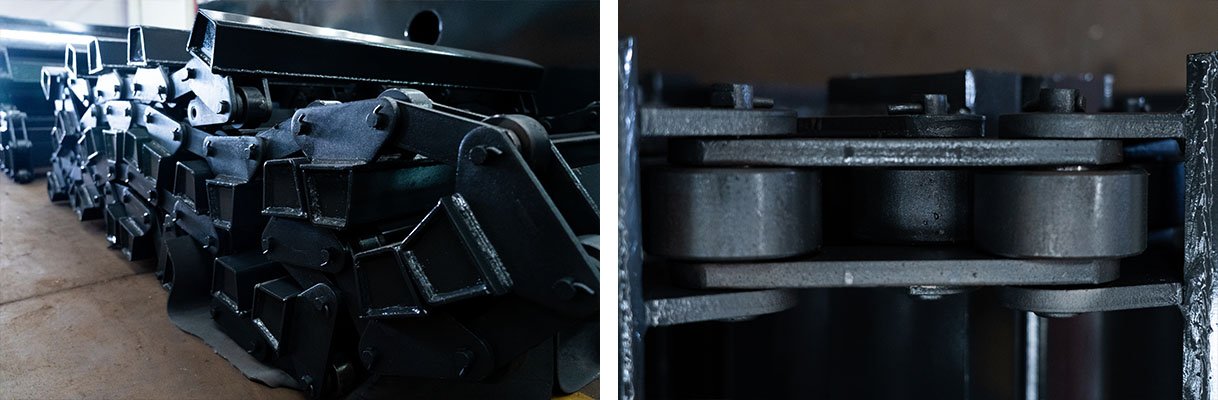
Wear Pad for Resistance
To ensure the wear pad would not be easily worn out by the track chains, we chose a special wear-resistant material NM400 for longevity. A high-quality material selection will extend the pontoon’s lifespan by 1-2 years on average.
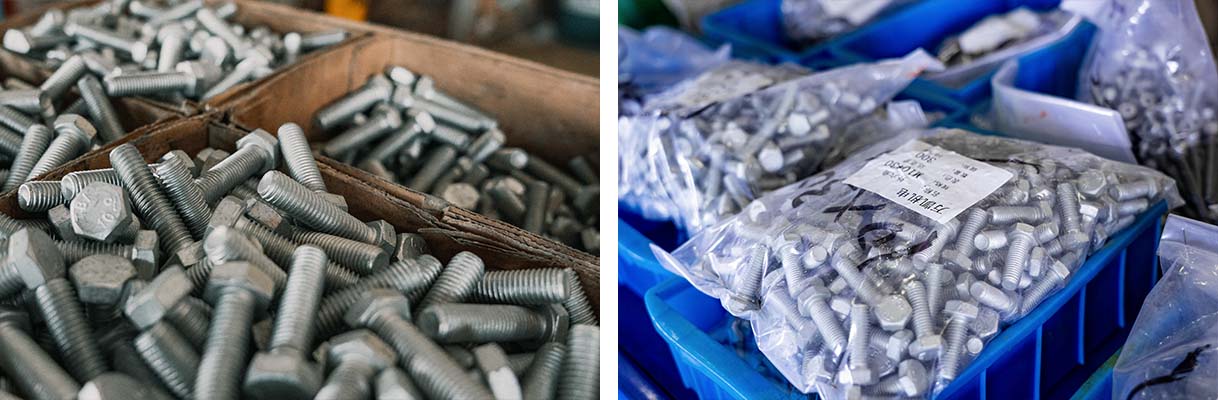
Screws Adopted for Amphibious Excavator
All screws equipped on our swamp buggy are treated with the Dacromet process and must go through a salt spray test which lasts for 1000 hours. This highly improves the anti-corrosion ability of the screws, and thus allows the excavator to work longer in a more severe working environment. The maintenance and replacement cycle of spare parts are thus extended.
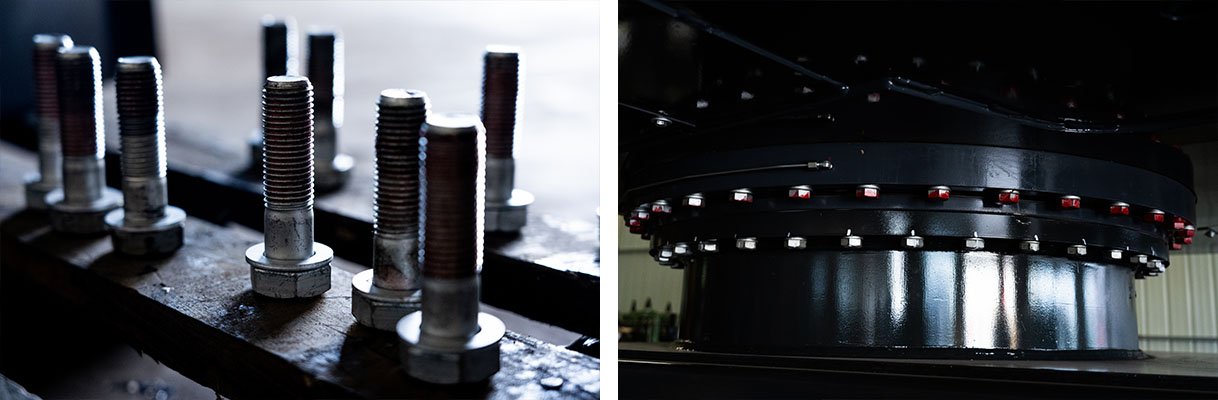
Hydraulic Oil Pipes & Fittings
The hydraulic oil pipe and fittings are imported from well-known brands with good durability, and the external surface of all oil pipes is coated with a protective layer of PVC to enhance their wear-resistant and corrosion-resistant properties. A tidy layout is maintained for all oil pipes in an orderly manner.
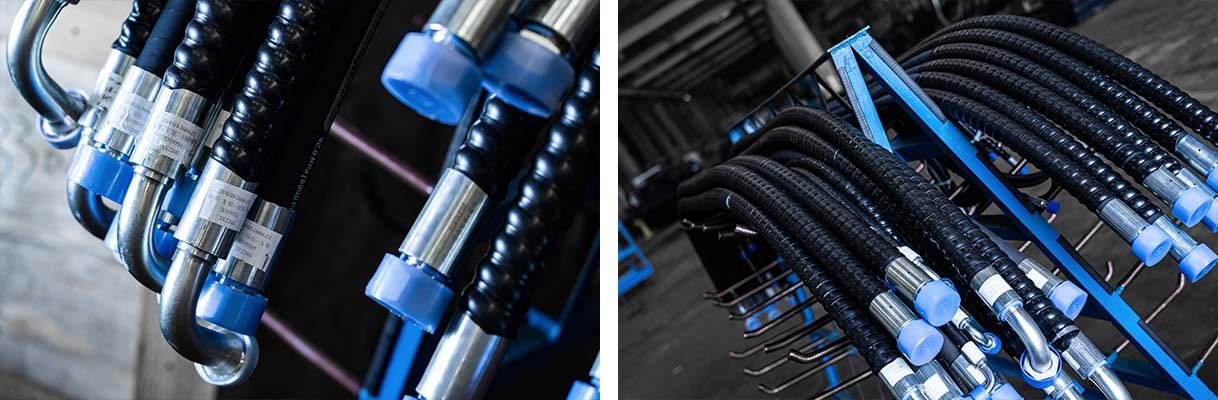
Guide&Drive Wheel Heat Treatment
To ensure reliable hardness and strength, both the front idler and drive sprocket of the PONTOON are specially heat-treated.
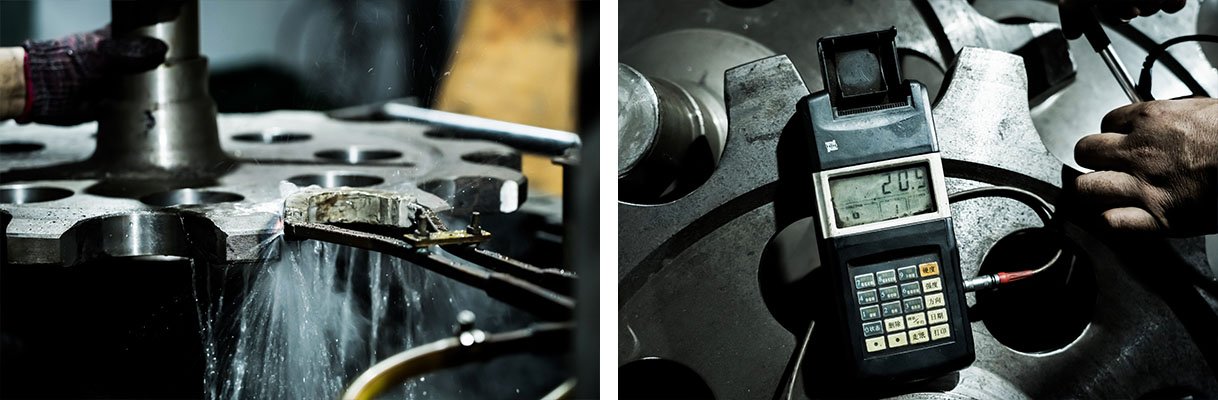
Why Choose RIVER’s Pontoon Undercarriage For Amphibious Excavators?
- Heavy duty processing equipment, better processing skills.
- High-precision equipment, excellence, quality Assurance.
- Robotic auto welding of pontoon undercarriage.
- More than 10 years of welding experience, meticulous and precise.
- The sandblasting process removes rust strongly, each pontoon must go through shot blasting till Sa2.5 grade with surface roughness within 30-70um before getting coated.
- Special paint for marine ships, the thickness of coating layer must achieve 160~200um and each pontoon must have 2 layers of primer and 2 layers of top coats.
- Each H-frame is machined as a whole by a gantry type machining center and the circle of bolting holes are milled by the hole milling machine.
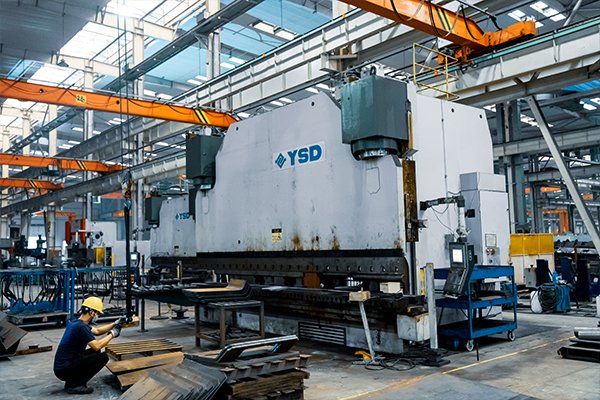
Cutting And Bending
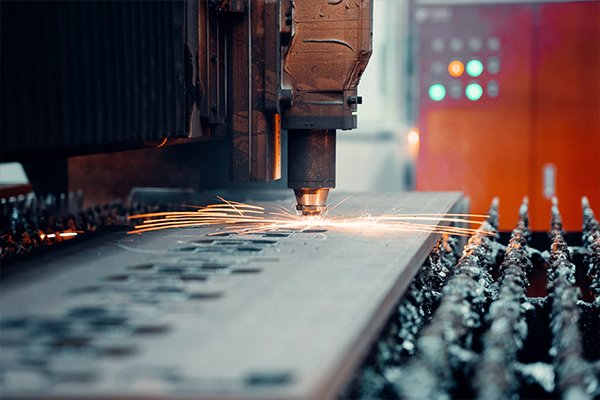
Plasma Cutting
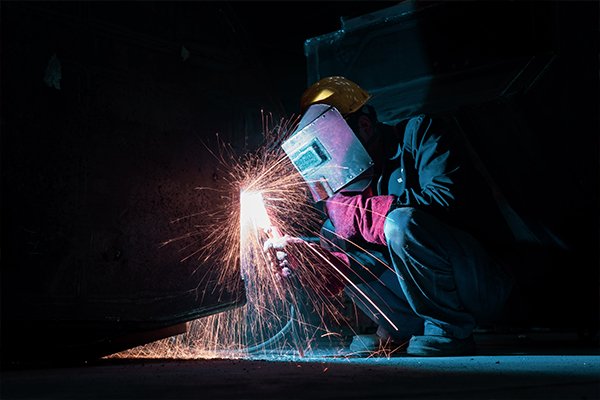
Welding
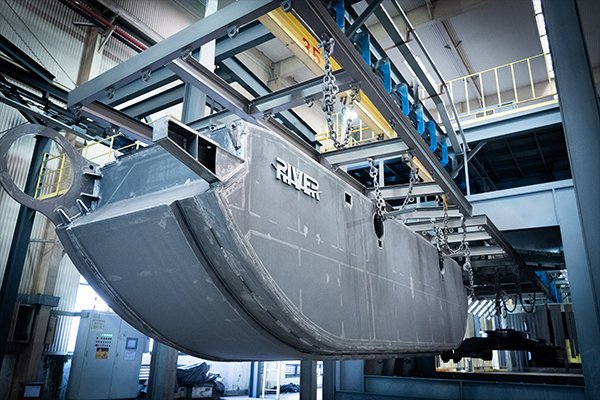
Sandblasting
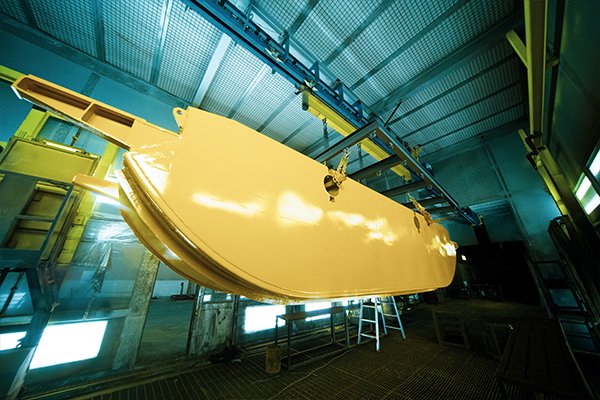
Spray Painting
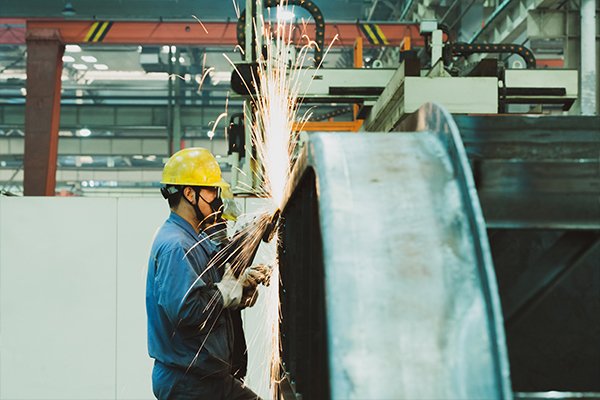
Polishing
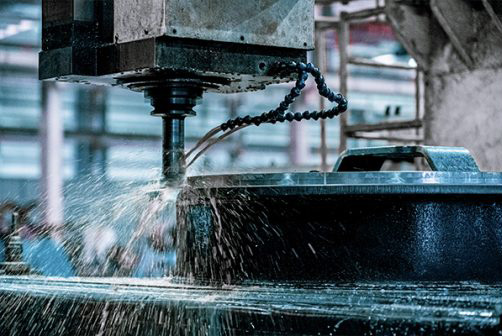
H-frame Machining
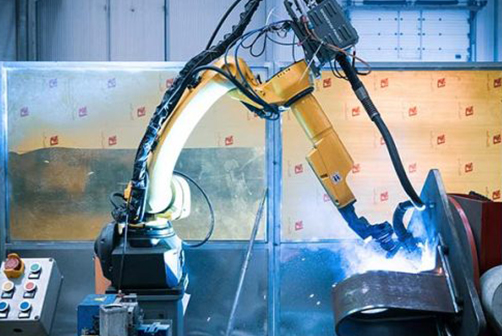
Robot Arm Welding
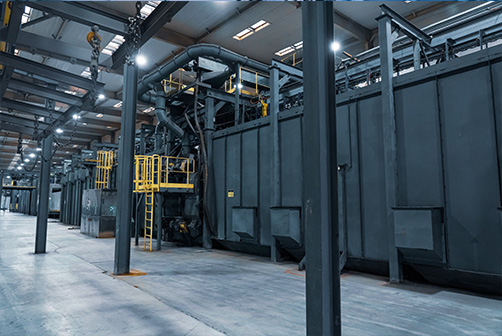
Fully Automatic Shot-blasting And Painting Line
FIND YOUR RIGHT SOLUTION FROM CHINA MANUFACTURER
Partner with RIVER MACHINERY for top-quality amphibious excavators and pontoon undercarriages. Fill out the form below, and our team will respond promptly to meet your project needs!